“This is where the magic happens,” says Harry Taroni, as he flashes a grin to the camera following him.
The 20-something metals trader bounds over to piles of discarded washing machines, cookers and other household appliances being unloaded from white vans in his family’s scrapyard in Birmingham, where they are known locally as the “scrap kings”.
Every day, the Taroni clan haggles over a steady stream of catalytic converters, brake discs and machine motors, as well as other items supplied by a colourful mix of “tatters” – Midlands slang for the crews who comb the streets looking for discarded metals.
On Thursday, a kilo of steel from bike frames or washing machines fetched about 18p (£180 per tonne), while brake discs are valued at 28p per kilo and car batteries about 58p, notes Hayley, Harry’s older sister.
Other finds are worth even more. Copper stripped out of cabling – known as “dry bright” to scrappers – is particularly sought-after, fetching £6 per kilo (or a whopping £6,000 per tonne).
“This is what we deal with all day long, bartering over pennies,” adds Harry, in a slick video published online. “But you know what? Pennies make pounds.”
To most people, these piles of thrown-away items are little more than junk. But the Taronis – and hundreds of recycled metal merchants like them – have made it their business to turn trash into treasure, processing it and selling it to the highest bidder.
It has made the family – which lives in a £3m country mansion – incredibly rich.
Others have made even more, with the little-known Sheppard family behind Warrington-based European Metal Recycling (EMR) thought to be near billionaire status.
One reason for their wealth is the growing demand globally for metals needed in the green energy transition.
And in the UK, business is now about to boom further as big steel makers switch over to electric arc furnaces (EAFs).
Unlike traditional blast furnaces, EAFs do not require coking coal or iron ore. Instead, their main input is something that Britain has in abundance: recycled steel.
In the UK, the technology is already being used by Liberty Steel and Sheffield Forgemasters, which make products for the aerospace and defence industries respectively.
Now, Tata Steel is set to switch the Port Talbot steelworks in South Wales – Britain’s biggest – to an EAF mill, while British Steel has revealed similar plans for its sites in Scunthorpe and Teesside.
The two companies produce more than half of the UK’s steel combined, with the changes triggering the loss of thousands of jobs.
Yet there will also be some winners, not least the 300 metal merchants nationally who will gain major new customers.
Currently, the UK produces around 11m tonnes of ferrous scrap. But just one-fifth of this is recycled, with the rest sent abroad to Turkey, Egypt, India, Bangladesh, Pakistan and other countries, which process it cheaply before exporting steel products back to us.
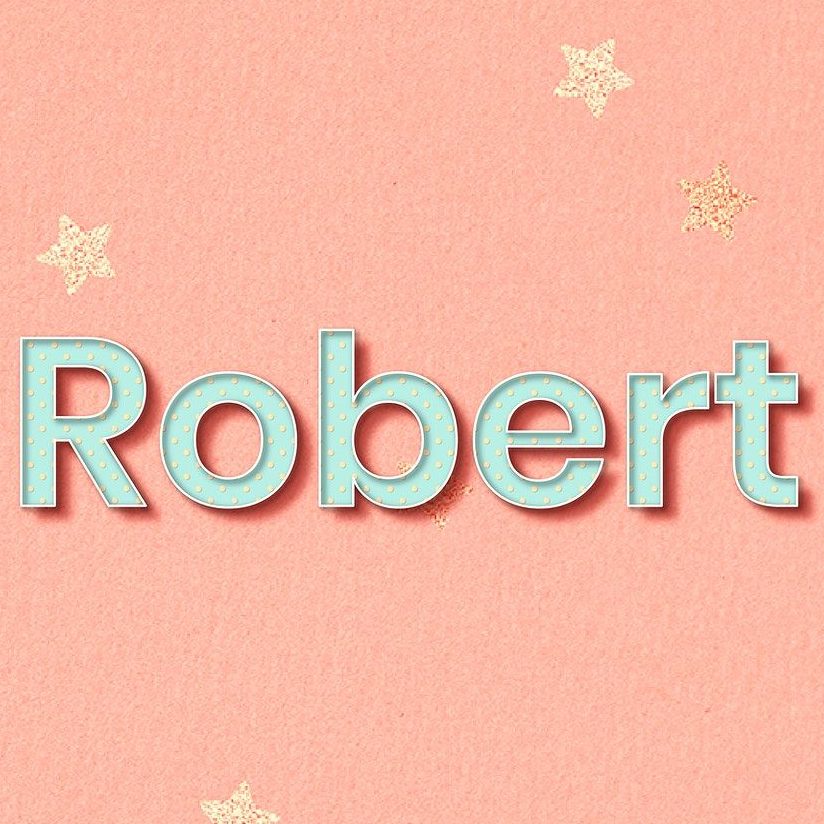
Robert Johnson is a UK-based business writer specializing in finance and entrepreneurship. With an eye for market trends and a keen interest in the corporate world, he offers readers valuable insights into business developments.